Hi! My name is Rob, and I’m a Mechanical Design Engineer living in Sydney Australia.
My mechanical design is blended with a unique understanding of technology (robotics) and skills in project management.
Please feel free to contact me for further information or to learn about projects that I can’t show online.
Bicycle Rack Design
This freelance project’s brief was to design and prototype a visually pleasing, minimal / simple bike rack to display a high end road bike on the wall. This work involved sketching hundreds of options and virtually testing (in Solidworks).
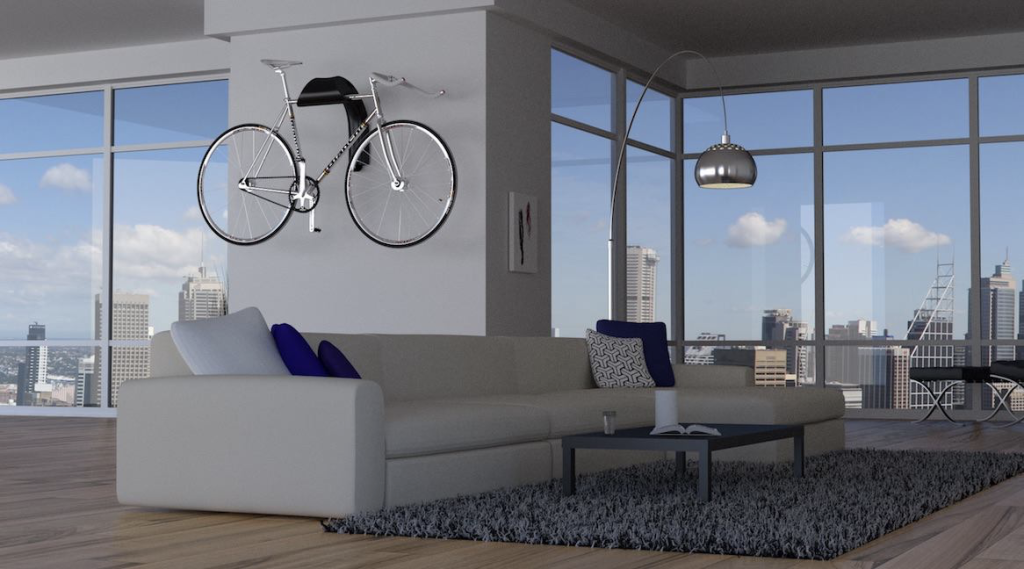
Blender was used to provide some semi-realistic images to help visualise the product in someone’s home.
The options were whittled down to a simple, visually pleasing natural spiral design with only two parts. The baseplate, made from folded steel is fixed to the wall and the spiral slides down over the top (hiding the bolts). Extensive back-and-forth with the manufacturer was required to satisfy any concerns and minimise costs.
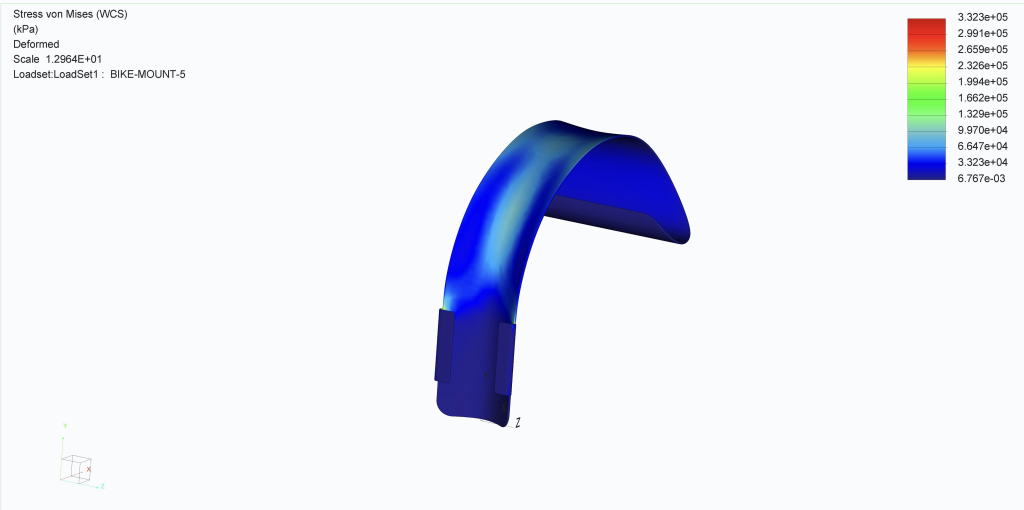
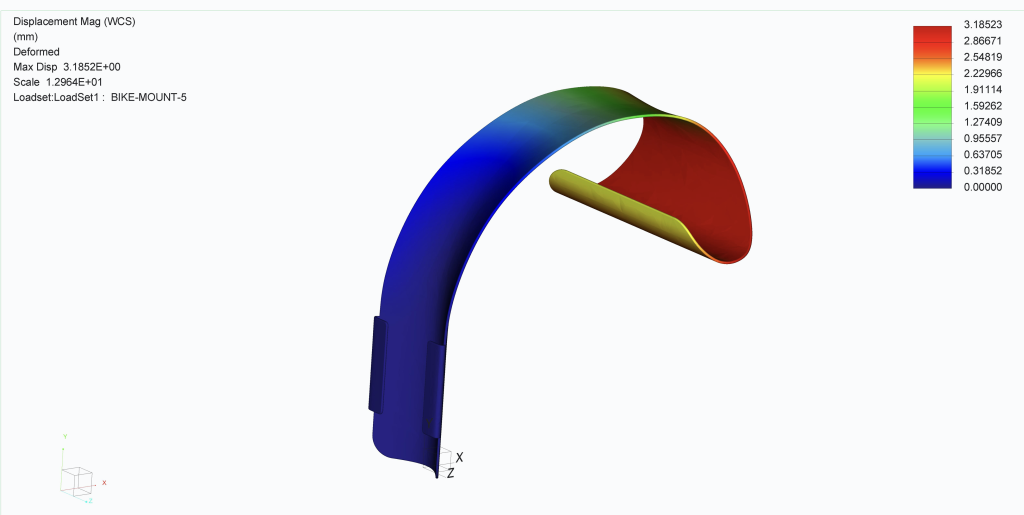
In this case displacement tests were performed to keep within a ‘window of desired give’. Stress tests were also performed and the result was a curved, durable bike rack finished with black powder coating.
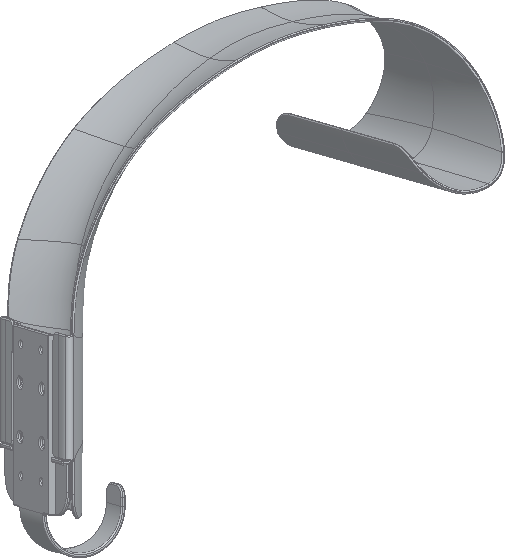
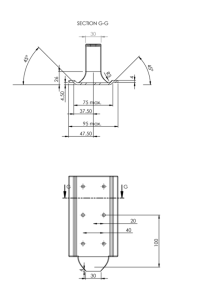
Materials and Changes: This product ended up being folded steel and the manufacturer was able to produce a seamless, beautiful finish. If I had complete freedom I would produce the curved part out of carbon fibre for the look and feel very high end bicycle owners appreciate. Also shipping would be greatly reduced if this arc component was very lightweight.
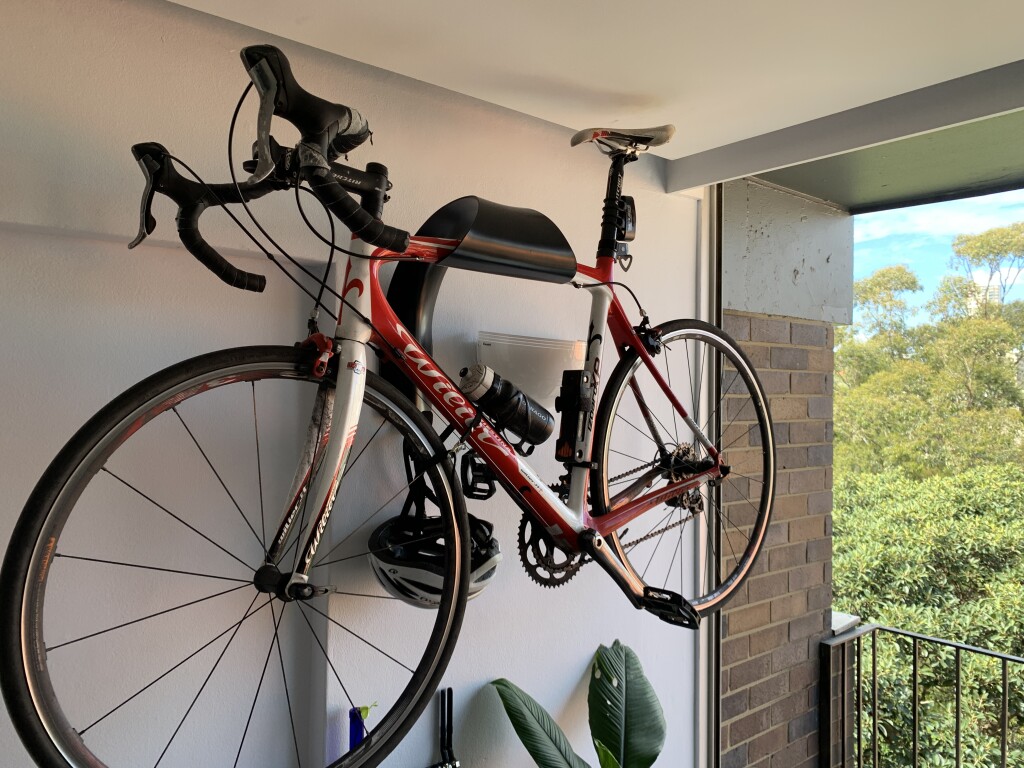
Reach Bravo
The Blueprint Lab Reach Bravo; A 7-Function all-electric waterproof robot arm. I am responsible for the mechanical design from ‘back of envelope’ concept through to teaching production how to assemble the arm. Customers required an arm capable of human-like movement and strength, capable of working submerged +300m below sea level.
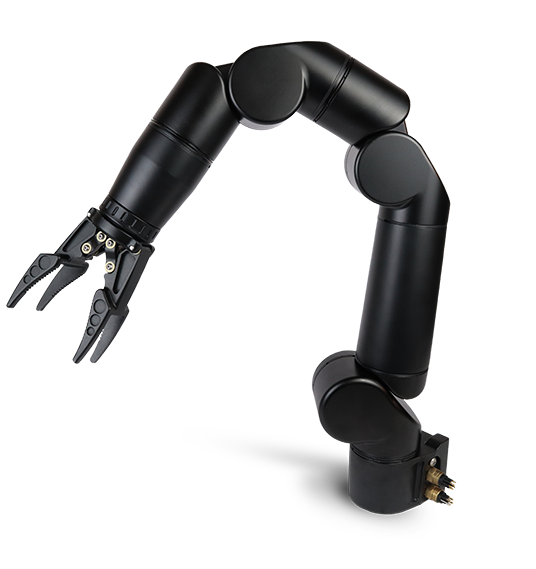
The modular design allows the arm to be used in any configuration from 6 degrees of freedom down to a simple single function grabber.
Patent: The design innovation I spent a long time developing was granted a patent. The unique tub shape of the joints resulted in a reduced number of o-ring seals and therefore a more reliable product, less prone to leaks.
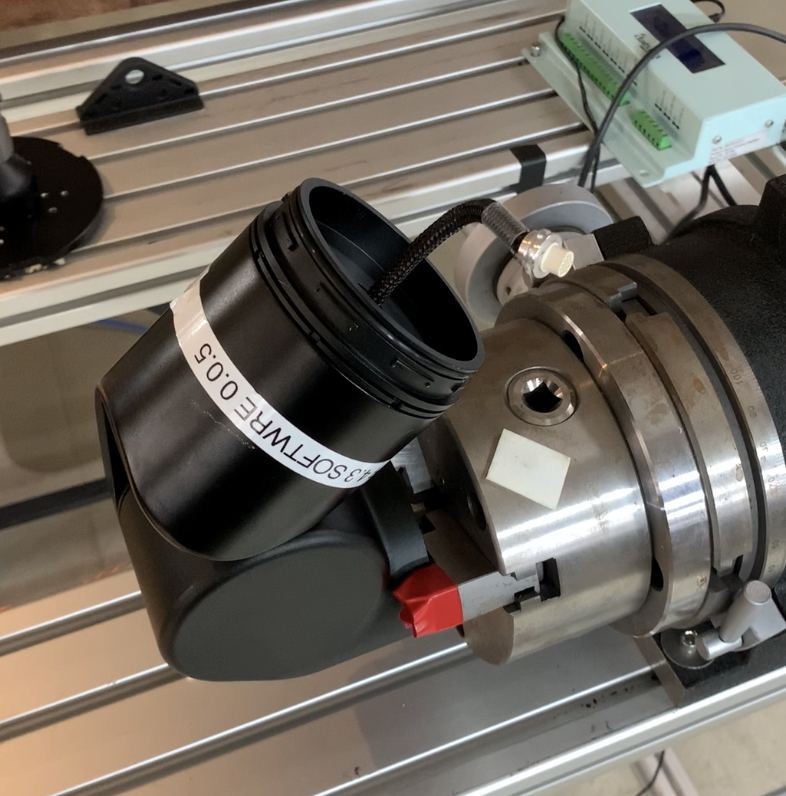
Each joint was modelled and tested within Solidworks before manufacture. All design tricks were used to allow for a factor of safety while reducing weight as much as possible.
The mechanical design included the selection of everything from motors to harmonic drive gearing to achieve the 12kg of lift at full reach. The team of engineers from different disciplines worked very closely to jam the electronics (including a full Ubuntu computer and sensors) into tight spaces. I really enjoy working collaboratively and achieving a top quality result.
Materials
The arm is predominantly milled Aluminium 6061 which was machined off site with hard black anodising for the finish. As they were made independently, 3D drawings of the many parts needed to be very high quality with all details such as finishes and realistic tolerances included. I was also exposed to plastic moulding design for custom plastic components, additive manufacturing and accommodating PCB’s/electronics.
Quality management systems were used, including my implementing PDM to keep track of every design iteration. Each version could be tracked to each customer such that if anything is damaged we would know which part was used.
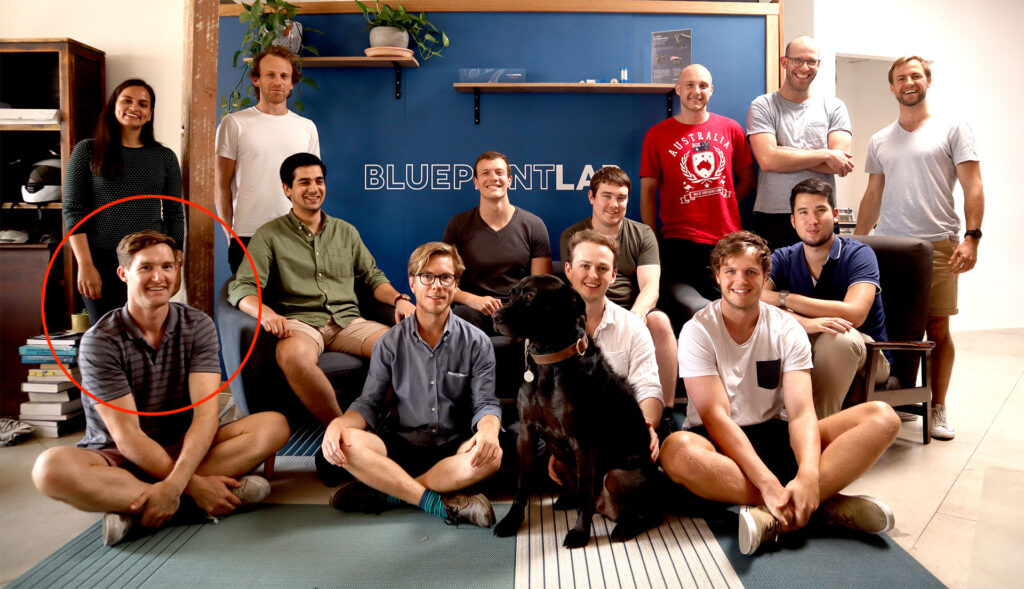
Wall Crawler
A hobby of mine is creating self driving robots using ROS and hacked parts such as xbox Kinect. I set myself a challenge to create a robot that could drive vertically.
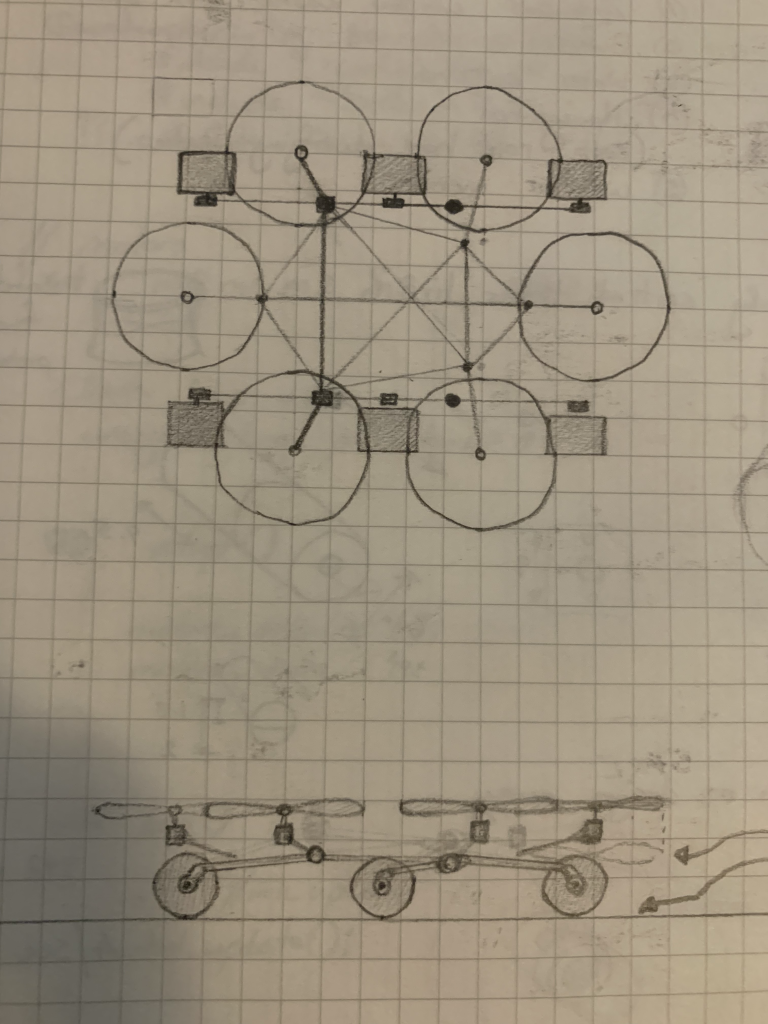
It was a good challenge. Of course the force created by the quad propellers needs to be higher than gravity * friction between the wheels and the wall surface so some foam wheels were used to increase this.
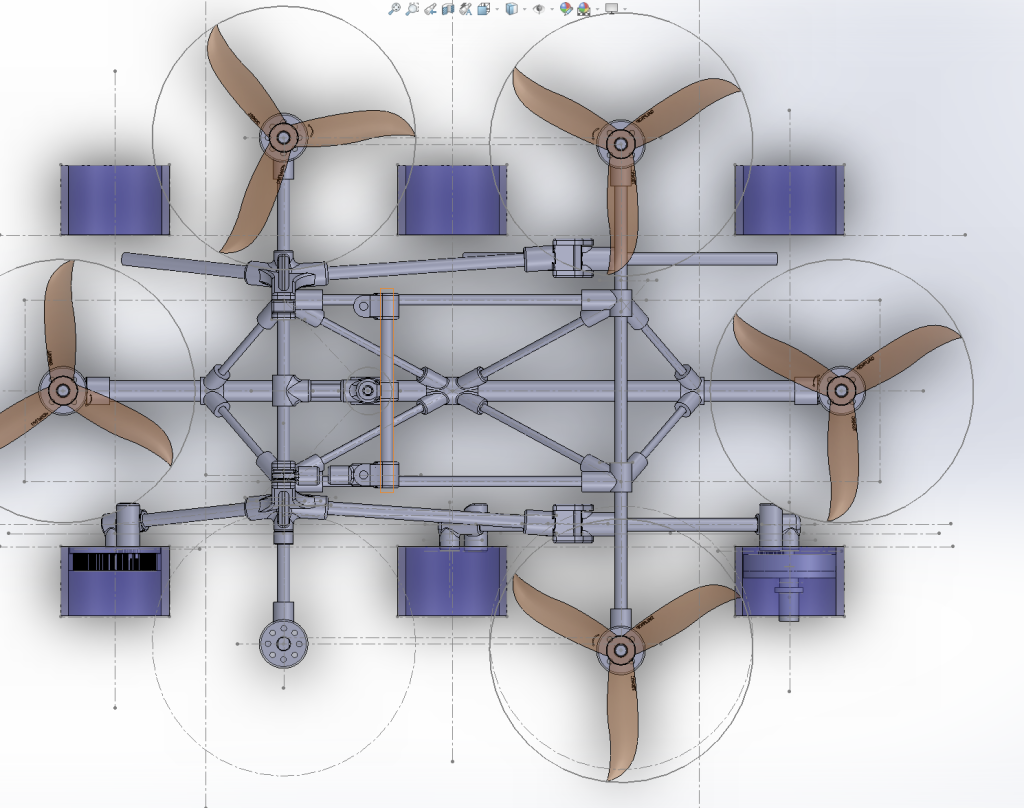
The rover has ‘bogey’ auto levelling style axels and each wheel has a small geared electric motor inside, so it is capable of negotiating bumps in the wall surface.
It needed to be as light as possible and so made from predominantly carbon fibre rods. My personal 3D Printer was used to make the lightweight plastic nodes. I successfully created a prototype that supports itself on a wall and drives around vertically. All the ‘brains’ needed to be off the rover with communication via the umbilical cord, to reduce weight.
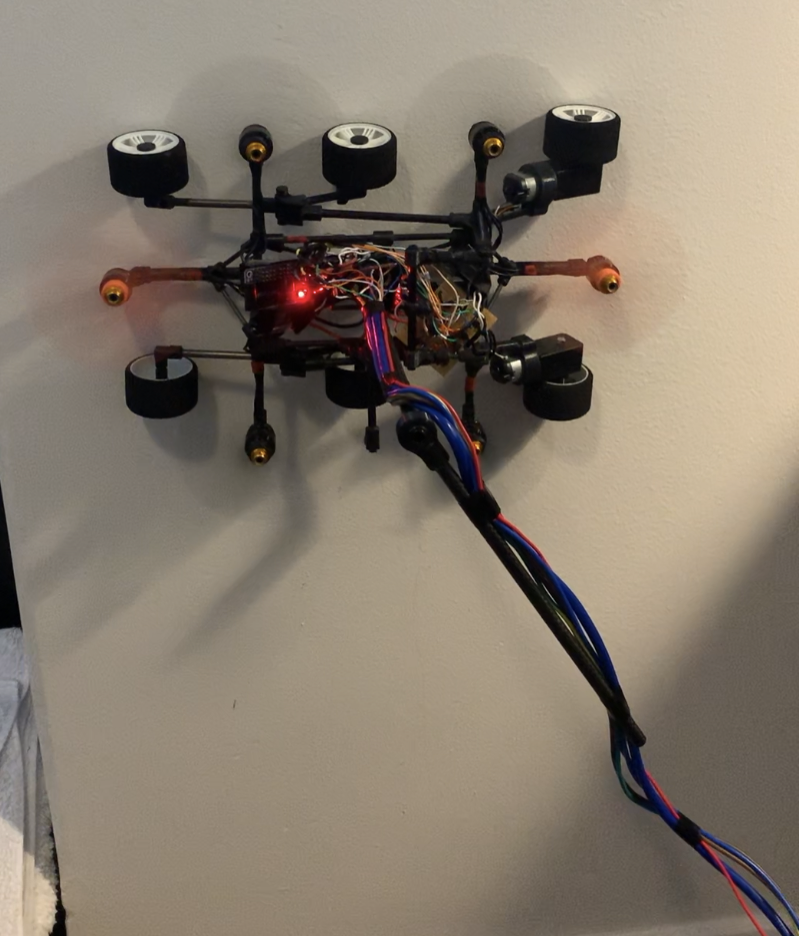
Changes: As this was a hobby project the
Working on challenging design problems is what excites me more than anything. With a strong appreciation of robotics and methods of manufacturing, I bring a unique point of view to a design solution.
Thanks for having a look at my work.